OEE improvement is critical to enhancing performance and productivity in manufacturing industries.
Understanding the components of OEE (Overall Equipment Effectiveness) can help you drive continuous improvement initiatives to boost equipment effectiveness and efficiency, resulting in increased profitability.
Measuring OEE Performance for Worksite Optimization
To calculate OEE effectively, it is essential to understand the three key components: availability, performance, and quality.
These elements should be measured using standardized data collection and overall equipment effectiveness software systems. Ideally, they should leverage IIoT software and automated, real-time data collection in order to save managers time.
By accurately measuring these factors, manufacturers can identify areas for OEE improvement and implement strategies to enhance their overall equipment effectiveness.
Here’s how to measure the components:
Equipment Availability
Availability measures the percentage of scheduled production time that a machine or system is available for use. It considers any unplanned downtime events, such as breakdowns or maintenance activities.
To calculate availability for OEE improvement, divide the actual operating time by the planned production time.
For example, if a machine was supposed to run for 40 hours and only ran for 32 hours, its availability is 80%.
Equipment Performance
Performance evaluates how efficiently a machine operates during its run time while accounting for losses from slow cycles, minor stops, and idling periods caused by operator inefficiency or equipment wear and tear. Equipment performance also measures the amount of time that equipment is sitting idle or unused.
To calculate performance for OEE improvement, divide the ideal cycle time by the actual cycle time multiplied by 100 to get a percentage value.
For example, if a machine should have a cycle time of 10 seconds but operates at 13 seconds, its performance is 77%.
Equipment Quality
Quality assesses the proportion of products produced without defects compared to total output generated during operation hours — essentially measuring first-pass yield rates in real-time environments where rework isn’t possible.
To calculate quality for OEE improvement, use this formula: good parts divided by total parts.
For example, if a machine produces 500 good parts out of 1000 total parts, its quality is 50%.
To measure overall OEE, multiply availability, performance, and quality together to get an overall percentage.
Industry Standards for OEE
Industry standards for OEE scores vary, but a score of 85% or higher is often considered world-class.
However, it’s essential to remember that improving your industrial worksite’s overall OEE score should not be the sole focus. Instead, concentrate on specific areas where OEE improvement would significantly impact productivity levels within an industrial worksite context.
10 Strategies for OEE Improvement
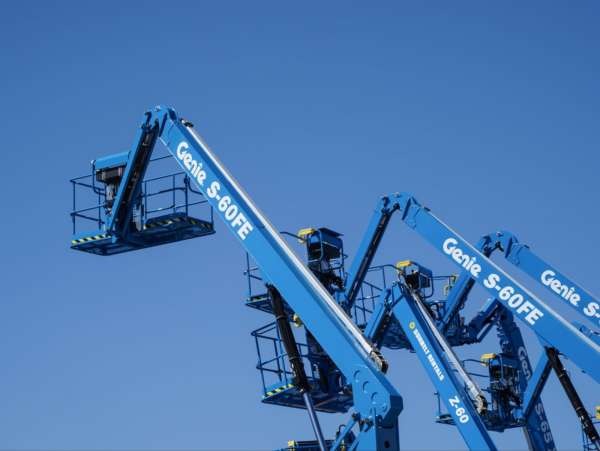
Implementing specific and actionable strategies can significantly enhance your operations and drive continuous improvement in your facility’s overall equipment effectiveness.
Here are ten practical approaches for OEE improvement:
- Establish a baseline
Establishing a baseline is a critical step in improving OEE. It helps identify current performance levels and determine necessary improvements to achieve specific goals.
- Monitor production trends
Regularly monitor production trends by keeping track of downtime events, slow cycles, and other anomalies that might indicate underlying issues with equipment performance or operation.
- Optimize equipment changeover time
Reducing changeover time between production runs is essential for increasing availability. Implement Quick Changeover (SMED) techniques, which streamline the process, minimize downtime, and lead to OEE improvement.
- Set SMART goals
Establish clear goals using SMART (Specific, Measurable, Achievable, Relevant, and Timely) criteria. Setting goals relevant to the organization’s broader objectives is essential for success. For example, if customer satisfaction is a top priority due to high defect rates, focusing on quality improvements would be more beneficial than solely targeting productivity increases through automation technologies alone.
- Reduce equipment downtime
Identify root causes of unplanned stoppages and develop preventive maintenance schedules based on these findings to reduce downtime and increase equipment efficiency.
- Improve operator training and knowledge
Well-trained operators can identify potential issues before they escalate into significant problems that impact productivity. Invest in continuing educational programs to guarantee personnel is up-to-date on the most recent techniques and advancements connected with their roles.
- Real-time production monitoring
Utilize real-time monitoring systems which allow you to track machine performance continuously, enabling faster decision-making processes when addressing inefficiencies or identifying opportunities for improvement.
- Embrace Total Productive Maintenance (TPM) and Lean Manufacturing principles
To improve OEE performance, adopting a comprehensive approach that encompasses both TPM and Lean Manufacturing principles is essential. These methodologies focus on maximizing equipment efficiency, reducing waste, and promoting continuous OEE improvement in industrial worksites.
- Encourage team collaboration
Promote team collaboration and foster a culture of communication and shared objectives. This will ensure everyone is on the same page and working towards the same goals, leading to better problem-solving capabilities and faster resolution times.
- Embrace digital transformation
Organizations can minimize manual errors during data entry tasks by automating data collection processes. Embracing an all-in-one equipment utilization monitoring solution such as Spot-r automates the data collection process so managers have real-time visibility into equipment usage and equipment downtimes within one intuitive dashboard.
TPM and Lean Manufacturing for OEE Improvement
Total Productive Maintenance (TPM) and Lean Manufacturing principles have long been regarded as two of the most important methods for improving efficiency, productivity, and quality in modern industrial settings.
While both approaches bring their unique advantages to the table, there is a synergy between them that you can leverage to maximize performance gains.
The synergy between TPM and Lean Manufacturing principles
To fully realize the benefits of both methodologies within an industrial worksite context requires a holistic approach that incorporates elements from each strategy.
For example:
- Create cross-functional teams comprising operators and maintenance staff members who work together on problem-solving tasks related to equipment efficiency or reliability issues.
- Promote open communication channels between departments so that information flows freely throughout your organization regarding potential areas for improvement.
- Incorporate real-time data collection through IIoT-enabled devices such as connected worker wearables into your facility’s operations management system (OMS). This allows you to track key performance indicators like OEE scores more accurately over time while identifying trends affecting overall production output levels.
Taking advantage of these synergies enables manufacturers to work toward OEE improvement and boost productivity levels throughout the entire organization.
Use IIoT Software for OEE Improvement
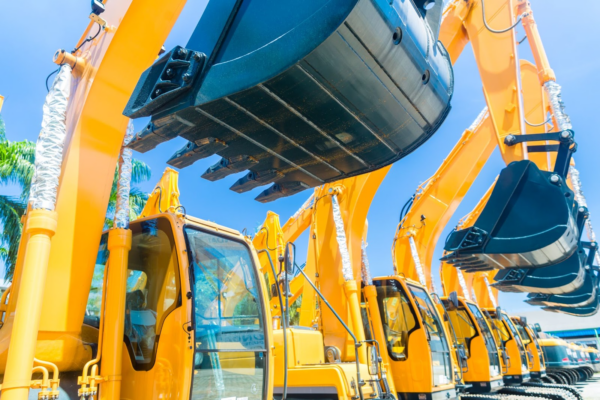
In today’s competitive landscape, embracing digital transformation is crucial for improving overall equipment effectiveness (OEE) and staying ahead of the curve.
By automating data collection processes through advanced software solutions, organizations can dramatically reduce manual errors during data entry tasks, streamline operations, and make more informed decisions.
Leveraging new IIoT software like Spot-r suite can help you in your pursuit to optimize your worksites’ OEE numbers. Our overall equipment effectiveness software solution provides a customizable and centralized dashboard with real-time data collection capabilities to put you in control of your equipment utilization.
To learn more about how Triax Technologies can facilitate OEE improvement through cutting-edge technology solutions like IIoT-enabled sensors or automation technologies, schedule a demo today.