Successfully Manage Turnarounds and Prevent Long Shutdowns
Managing industrial turnarounds and shutdowns can be difficult. A large influx of contract workers, combined with low visibility into both people and equipment present major roadblocks to productivity. This can lead to delayed turnaround times and longer shutdowns, resulting in huge costs and production losses.
The Spot-r® IIoT software is designed to mitigate your turnaround and shutdown concerns. It combines automation, real-time monitoring, and comprehensive analytics to improve every aspect of site management, helping refineries prevent delays and oversights. Focused on work-level data capture and insights, our IIoT platform helps managers stay agile, respond quickly to hazards or emergencies, and prioritize on-site safety—automatically and in real-time.
Let Spot-r help you realize a new level of efficiency, cost savings, and safety standards during a crucial time in your operations.
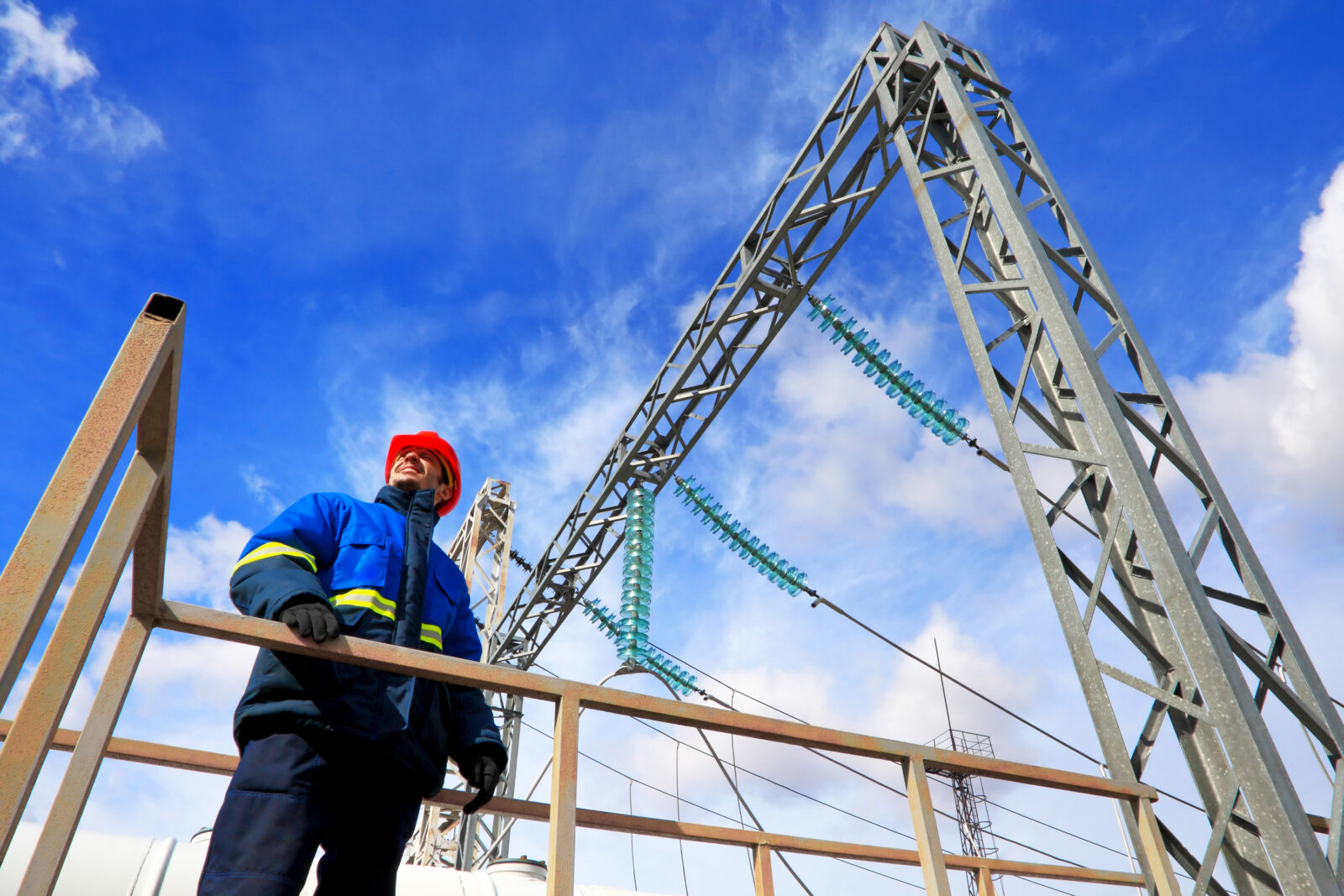
What are the Benefits of Implementing an IIoT Software Solution to Optimize Turnaround Time?
During a turnaround or shutdown, all or part of a site is taken out of service to perform necessary work that cannot be done during normal operations, temporarily causing a shift in the allocation of resources and hours available to conduct work.
An efficient turnaround requires a detailed plan outlining the scope of work, the duration of the shutdown, the resources required, and the safety protocols that must be followed. The faster labor resources are able to complete these tasks, the quicker the site can resume normal operations.
Triax gives worksites all the visibility and analytics needed to decrease costs and increase efficiency. By leveraging the Spot-r IIoT software solution, site managers gain real-time visibility into all people and equipment that are onsite doing maintenance, repairs, upgrades, or other modifications. This creates a more connected site, assists with labor forecasting, improves equipment management, and helps you meet and maintain OSHA emergency preparedness requirements.
Spot-r gives you the data and analytics to effectively optimize turnarounds and shutdowns
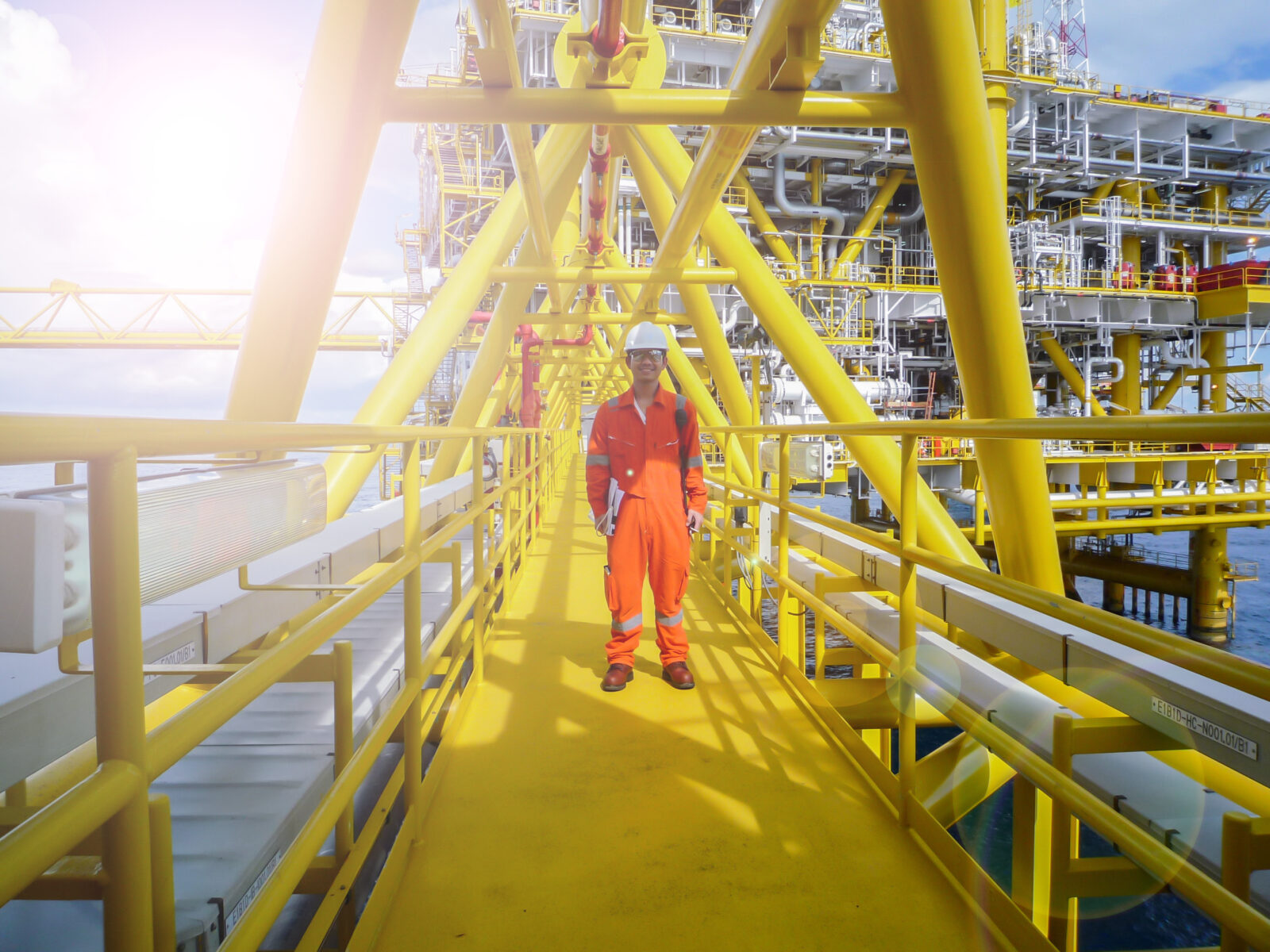
Case Study
Learn How Worley Improved Efficiency for Thousands of Temporary Workers
Managing a large team of contract workers for pre-turnaround work comes with a host of logistical challenges. Triax helped one contractor identify pinch points and regain thousands of lost worker hours resulting in a faster turnaround at an INVISTA petrochemical plant in Texas.
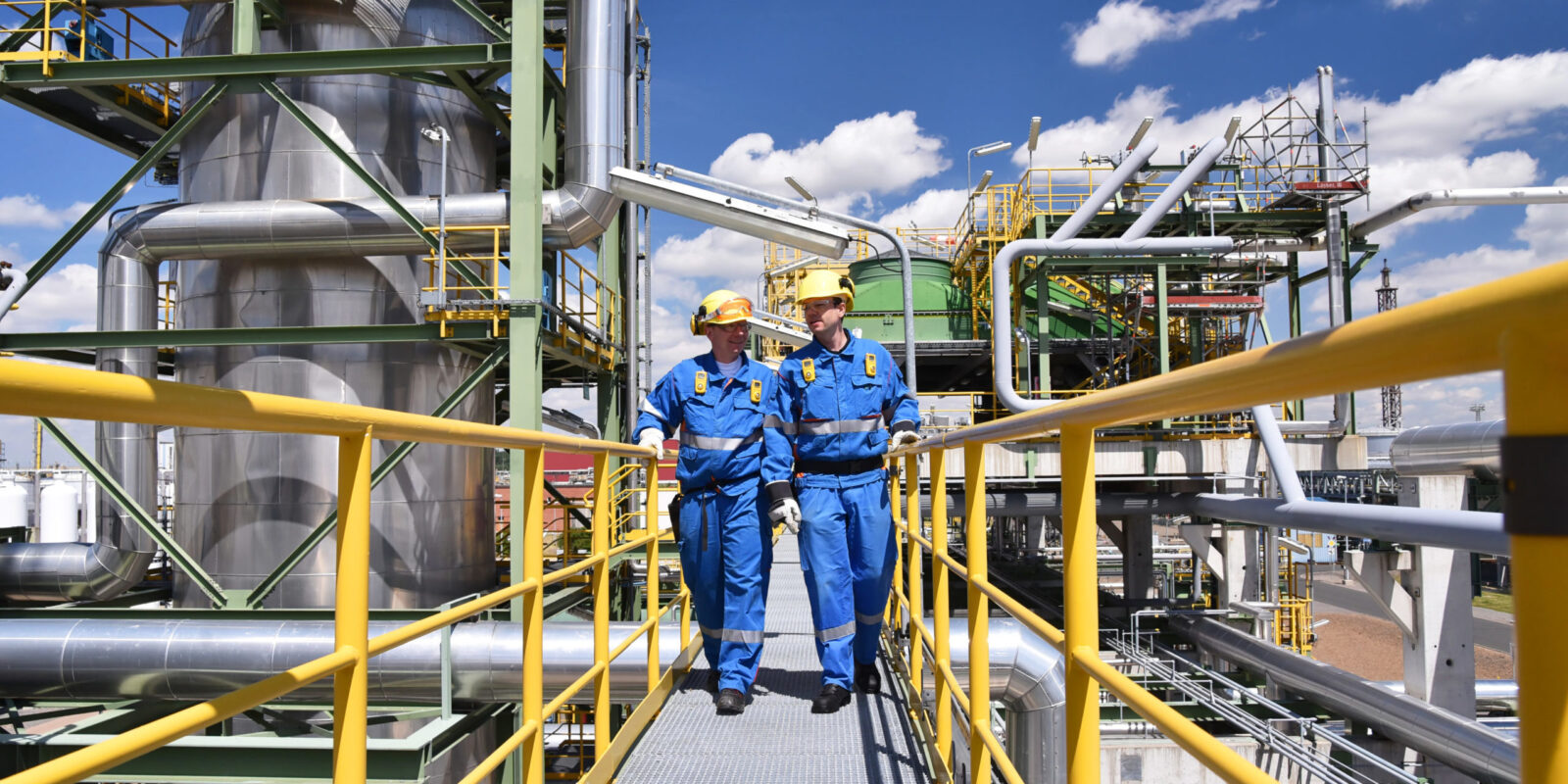
“Digital technology, like wearable devices and Spot-r, offer great potential to improve safety and productivity on worksites. But when technology like this is combined with our team’s intimate knowledge and experience of our customer’s site and workforce, the outcomes are transformational.”
Rahim Ghassemi, Business Manager at Worley
More Spot-r Use Cases for Turnarounds
Learn more ways Triax can help save money, increase productivity, and improve worker safety–during both turnarounds and regular operations.
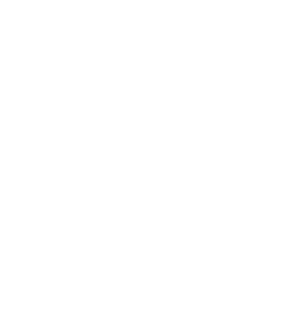
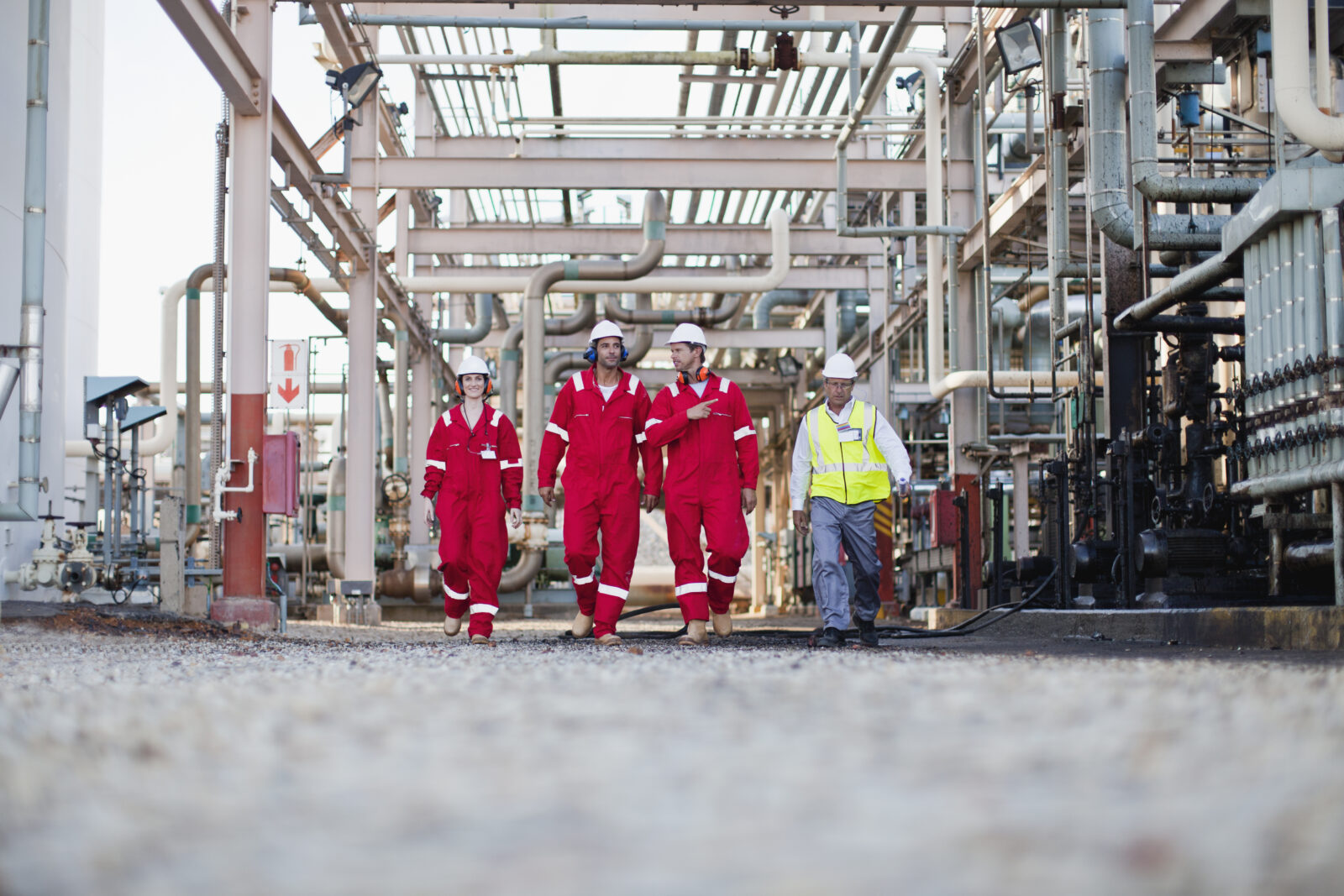
Safety and Emergency Management
Enhance safety measures by implementing features such as two-way notifications, remote site security management, real-time fall detection, and automatic evacuation and muster protocols.
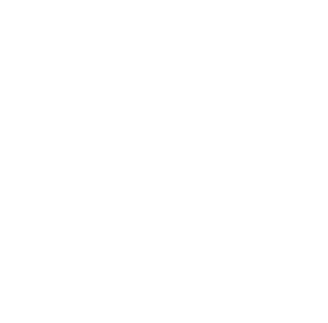
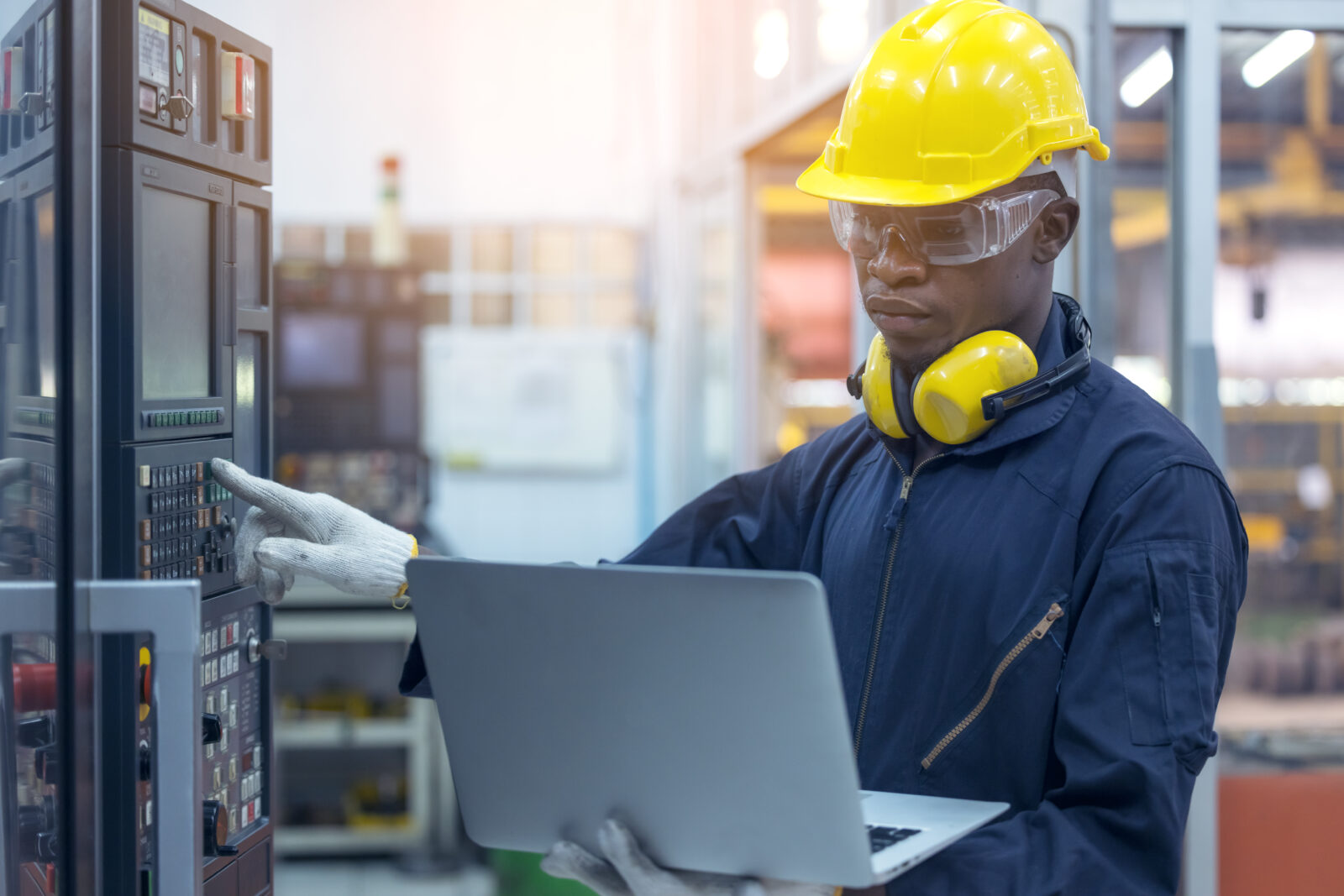
Equipment Monitoring
Unlock unparalleled visibility and real-time insights into equipment usage, resulting in cost savings and improved refinery productivity.
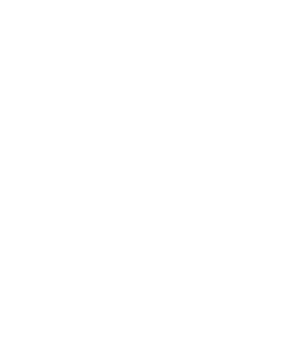
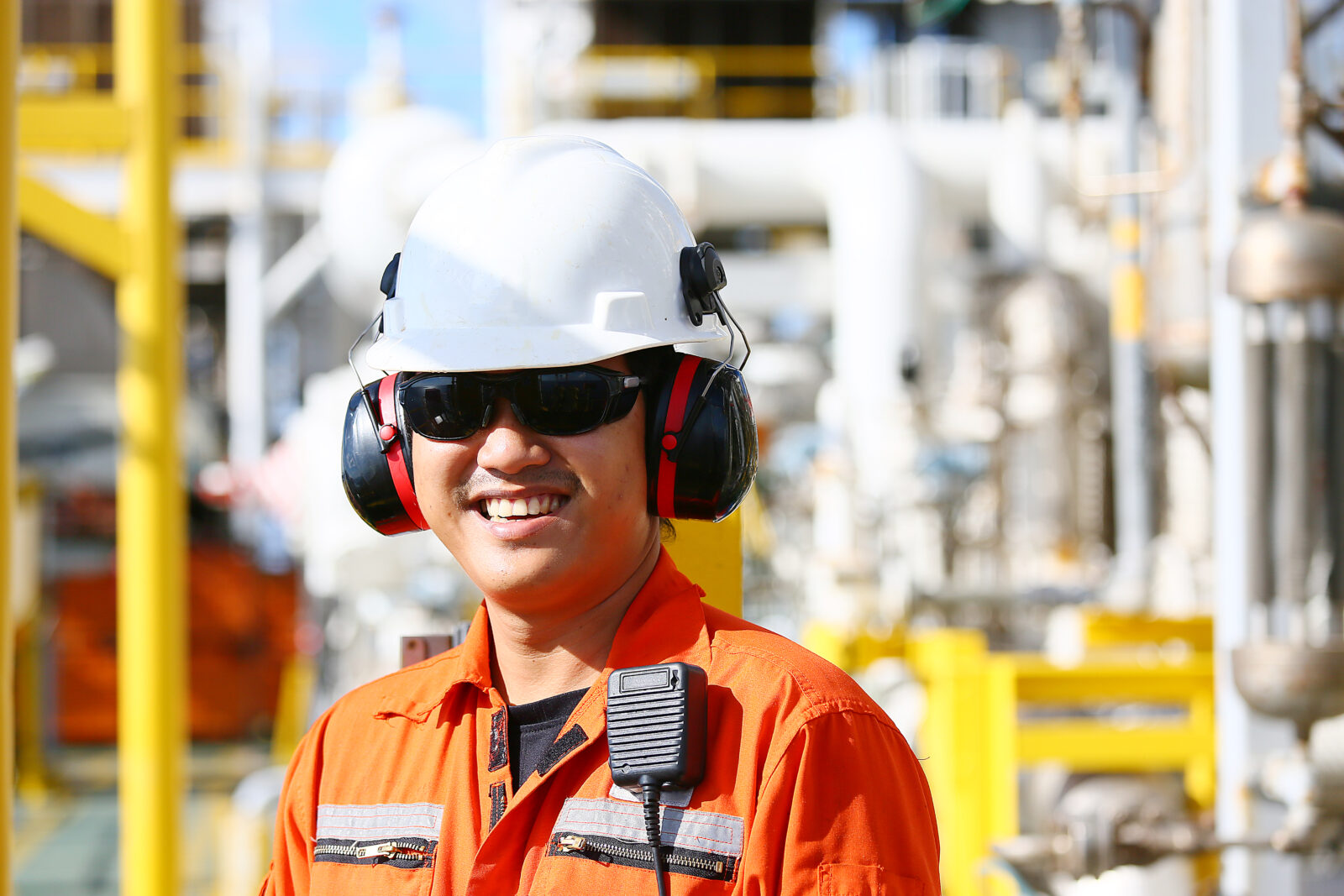
Connected Worker
Keep onsite workers safe during turnarounds, shutdown protocols, and normal operations with worker safety wearables and automated monitoring.
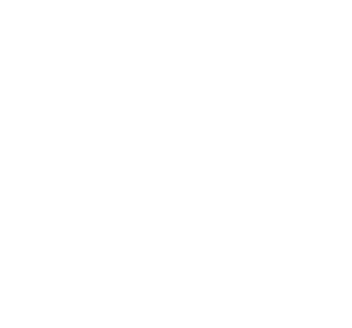
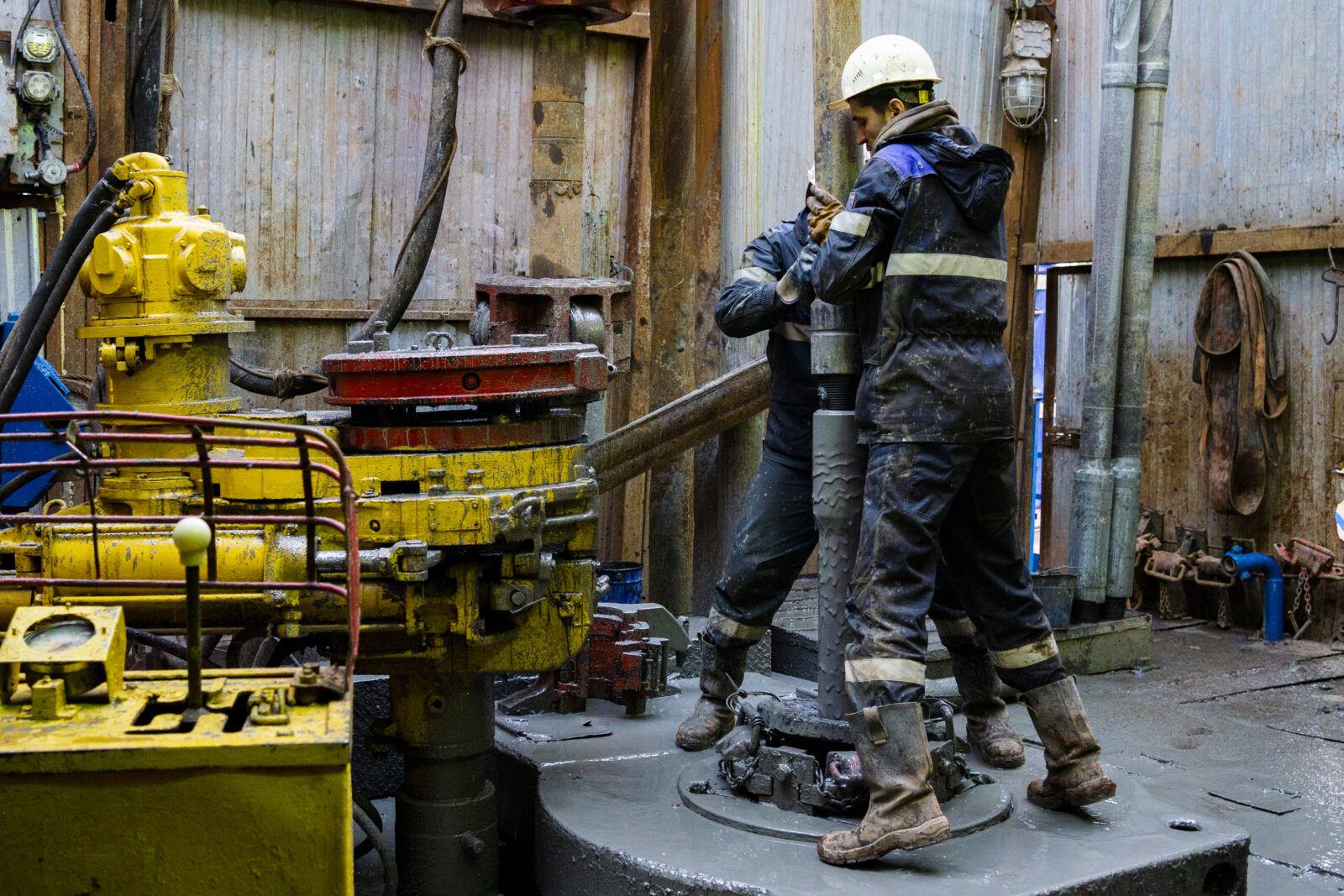
Labor Productivity
Identify pinch points, adjust schedules, and streamline operations in order to improve productivity in your refinery.
Ready to See How Triax Can Help During a Turnaround or Shutdown?
Sites are able to immediately realize the benefits of our Spot-r IIoT software after setup. Contact us today to get connected with a dedicated Client Success Specialist today, who will help with your IIoT setup, customization, and onsite implementation.
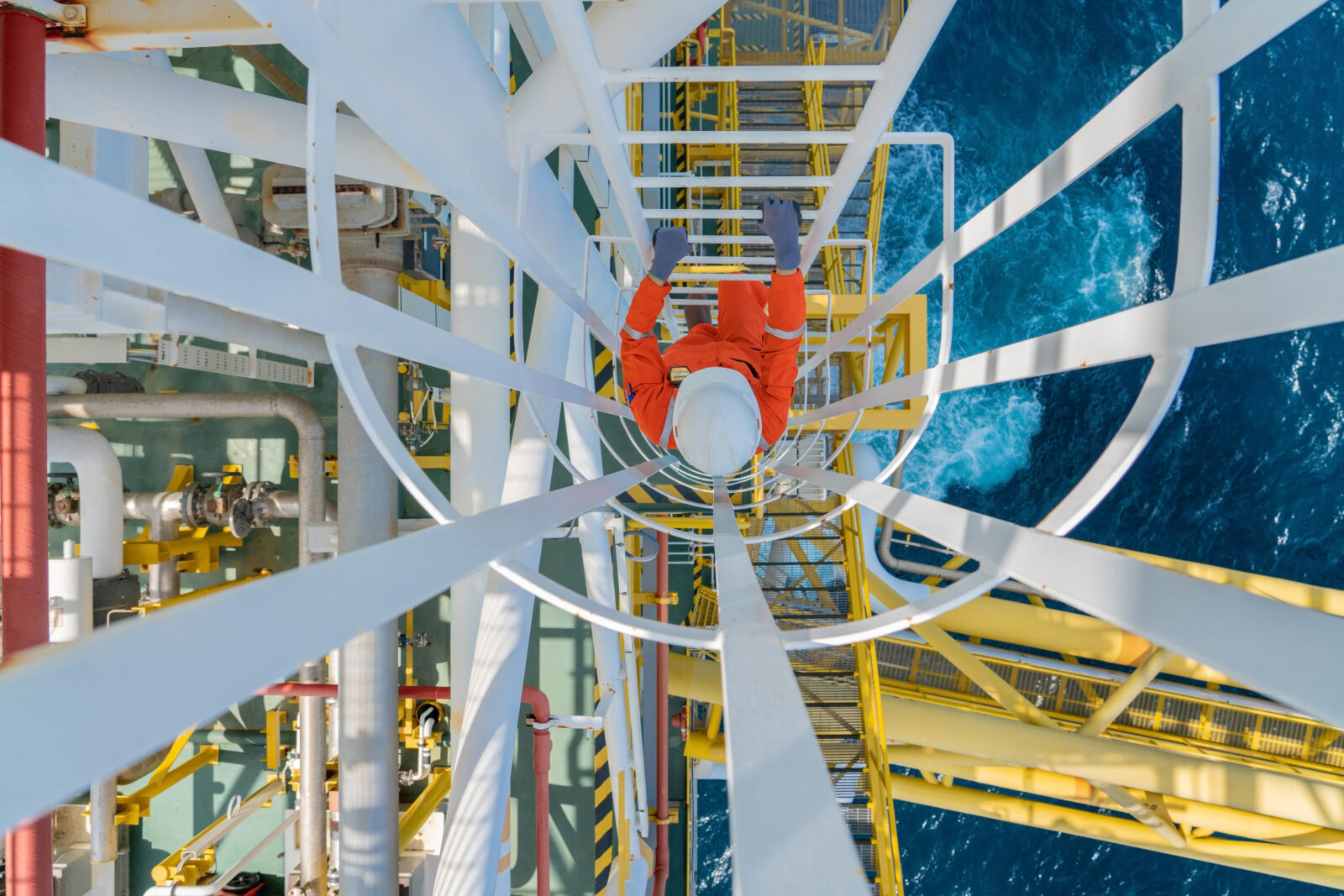