As technology continues to advance at an unprecedented pace, digital twin software has emerged as a revolutionary approach to optimizing and streamlining various aspects of an industrial worksite.
What is a Digital Twin?

In simple terms, a digital twin is a virtual replica of a physical object, process, system, or environment. It is a computer-generated model that uses real-time data and advanced simulations to create an accurate model that mirrors its real-world counterpart, including its physical characteristics, behavior, and performance.
An example of a digital twin use case might be a frac pump, which can be used to simulate how it operates in different weather conditions and predict maintenance needs. Meanwhile, a digital twin of a building can be used to optimize its energy consumption and environmental performance.
What Is A Digital Twin Also Known As?
A digital twin may also be called a cyber-physical system (CPS) or “twinning.” These terms emphasize the connection between the virtual model and the physical one while highlighting their interdependence.
Let’s break this definition down even more to illustrate some specific use cases.
How Can Digital Twins Be Used In Industrial Fields?
In the industrial sector, digital twin and IIoT technologies allow for real-time monitoring, analysis, and optimization of nearly every aspect of a worksite.
- Data collection: Sensors installed throughout the physical environment collect various types of information like temperature readings or equipment status updates.
- Data processing: The collected data is processed by sophisticated algorithms that analyze patterns and trends to predict future performance.
- Data visualization: Real-time data from digital twins can be visualized in user-friendly formats such as graphs or charts so decision-makers can easily understand what’s happening at any given moment.
- Actionable insights: Based on these visualizations, users can identify areas for improvement within their operations — whether it’s adjusting machine settings for optimal output or scheduling preventive maintenance before costly breakdowns occur.
Digital twin IoT enables organizations to join their physical resources with the digital realm, offering a more comprehensive understanding of their activities and the ability to be more agile with their decisions.
The Top Industries That Have Been Revolutionized by Digital Twin Technology
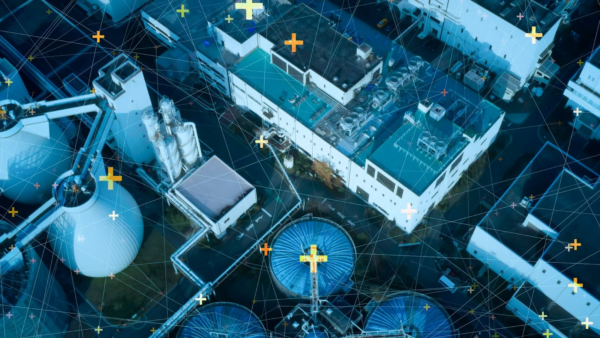
There are many industries and companies using digital twins – and there is no limit to the technology’s practical applications. But these are some of the industries that have seen the most transformation in recent years:
- Manufacturing: Digital twin IoT is used to monitor and optimize production lines, reduce downtime, improve product quality, and enhance overall efficiency.
- Construction: Digital twins help construction companies effectively plan projects, map out new builds, and manage resource allocation, risk assessment, and progress tracking.
- Mining, chemical, oil, and gas: These sectors can use digital twins to enhance their safety measures, track machinery performance, and proactively perform equipment maintenance to minimize operational disruptions.
- Logistics and transportation: Digital twin technology can be applied to simulate the movement of goods, including vehicles, routes, and schedules, optimize warehouse layouts, plan storage capacity, and predict vehicle and equipment maintenance.
Benefits of Leveraging Digital Twin Technology
Industrial sites that implement digital twin technology often see improved efficiency, productivity, safety, and security.
More Efficient Worksites
With access to real-time data from the physical assets and processes within an industrial worksite, managers can quickly identify bottlenecks or inefficiencies. This allows for prompt corrective actions that optimize labor productivity and minimize downtimes.
Enhanced Labor Productivity
Industrial worksites are large and complex, and often have thousands of workers on-site. Keeping track of workers is crucial for enhanced productivity and safety, but it’s difficult to have full visibility into worker behavior in all areas of the worksite with standard CCTV systems.
Digital Twin technology isn’t just limited to buildings, it can also include wearable technology. Adopting a wearable digital twin technology solution for all workers allows site managers to quickly identify labor productivity at the individual level, and compare this to an average. Site managers gain the critical visibility they need to see when and where labor productivity is suffering, and where bottlenecks are occurring on the worksite.
More Informed, Agile Decision-Making
A digital twin provides a comprehensive view of the entire worksite’s operations. This enables directors and supervisors to make more informed decisions by analyzing performance metrics in real-time, such as overall equipment effectiveness or production outputs.
Longer Equipment Lifespans and Fewer Breakdowns
Digital twins give you the ability to monitor the lifespan, working times, and general functions of all worksite machinery, equipment, and vehicles in real-time. And that allows managers to plan extremely accurate, predictive maintenance schedules.
Outstanding Safety Improvements
Real-time monitoring via a digital twin helps ensure worker safety by identifying hazards early on and allowing for swift intervention when necessary. Additionally, it supports training efforts by providing detailed information about safe operating procedures, evacuation routes, and mustering station locations.
Faster Time-to-Market Cycles
The manufacturing industry has seen accelerated product development cycles with digital twins. It allows rapid prototyping through virtual simulations instead of building multiple physical models, which can be both time-consuming and costly.
Improved Product And Building Quality
By simulating various scenarios with digital twins during product and building design stages, engineers can test different configurations without having to build physical prototypes — saving time and resources while ensuring optimal quality control measures are implemented throughout the entire production process.
Better Data-Driven Innovation
By collecting and analyzing data from a digital twin, companies can identify trends and patterns that may lead to new opportunities for innovation. Many benefits of digital twins may yet to be discovered for your specific worksite!
Unlock More Opportunities With Digital Twin Technology And Triax
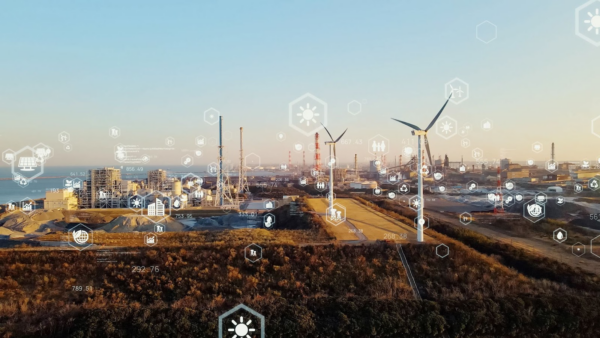
Looking ahead, digital twin technology will continue to reshape industrial operations and revolutionize manufacturers’ businesses. We’ve only begun to see all the possibilities for incorporating digital twins into new industries and worksites.
But the need to adopt digital twin and IoT solutions is becoming increasingly essential as industries continue to evolve in response to the latest technological advancements.
The benefits it provides help organizations stay competitive in an ever-changing landscape. And the Spot-rTM IIoT platform is at the forefront of this revolution by offering comprehensive IIoT software that leverages digital twin solutions for improved industrial operations.
At Triax, we understand that every operation is unique.
We’ve built our solution to meet the unique safety and productivity needs of large industrial worksites. It is entirely customizable to your site and centralized in one intuitive, encrypted dashboard, making it easy for managers and supervisors to do real-time monitoring and quickly extract insightful data.
Book a demo today!