Blog
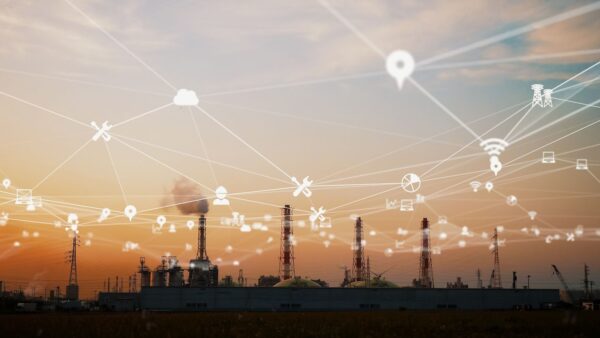
Top 6 Applications of Digital Twins in the Manufacturing Industry
Digital twin technology in the manufacturing industry allows for real-time monitoring, analysis, & optimization of nearly every aspect of a production line.
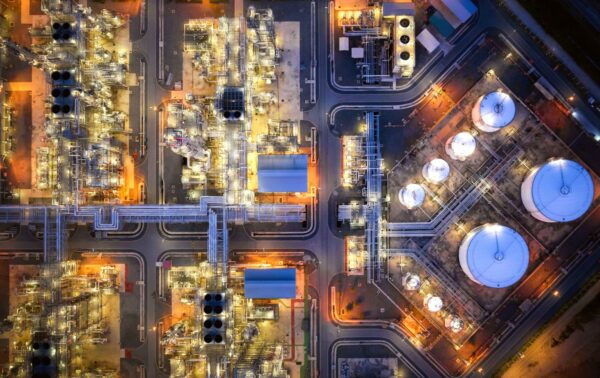
How Industrial Sites Can Improve Turnaround Management and Planning
More than 30% of all turnarounds experience scheduling delays. See how your organization can improve turnaround management with these strategies and tools.
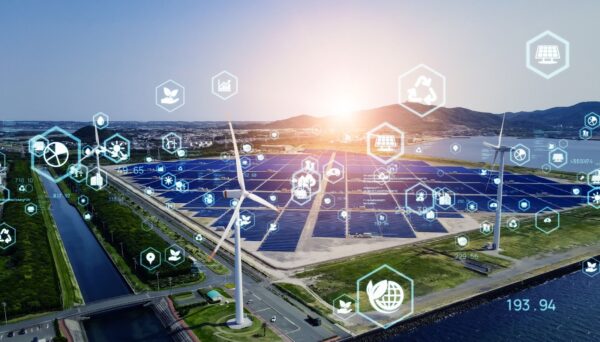
5 Solutions Leading Digital Transformation in the Energy Industry
As the energy industry is transitioning to renewables, digital transformation in the power and energy sectors is more crucial now than ever before.
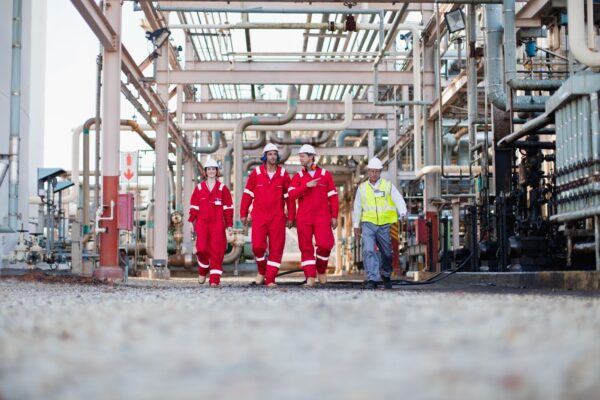
Do You Know Your Worksite Labor Efficiency Variance?
Labor efficiency measures how well employees accomplish tasks in comparison to industry standards. To calculate it, use this labor efficiency variance formula.
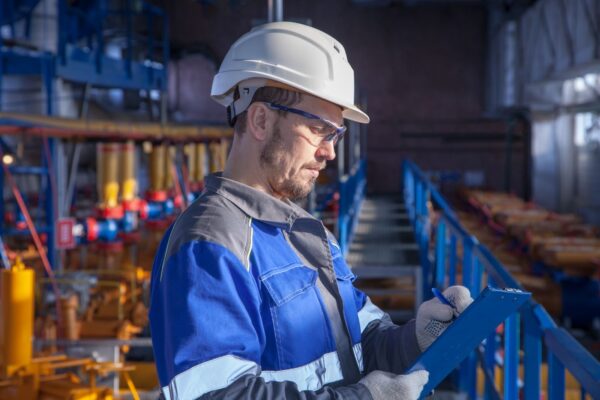
How is Labor Productivity Measured on Industrial Worksites?
Labor productivity is measured by evaluating the efficiency of workers in producing goods or providing services. Learn how it’s measured on industrial work sites.
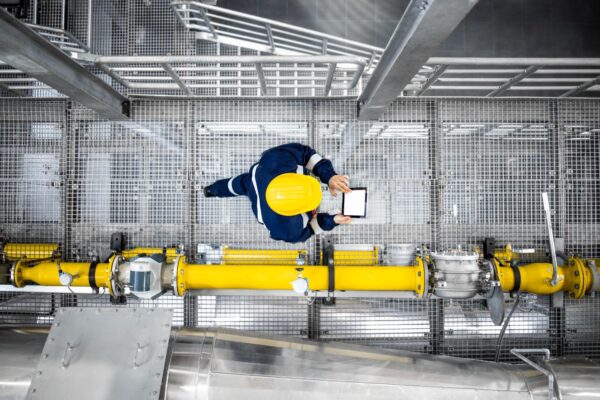
8 Benefits of Automating Plant Labor Operations Management
Learn how and why adopting an IIoT platform with powerful automation features drastically improves and streamlines plant operation management.
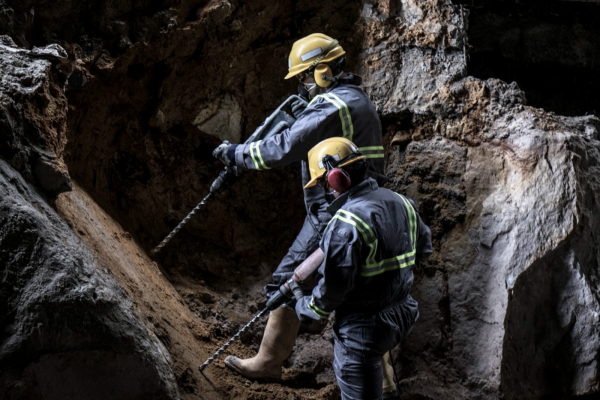
How IoT in Mining is Changing the Industry: Devices, Examples, and Use Cases
The development of IoT in mining has changed how operations are handled, effectively reduced workforce needs, and improved overall accuracy. Learn more.
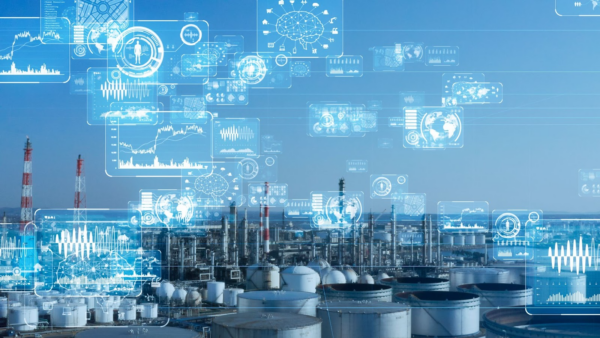
What is a Digital Twin and What are the Benefits for Industrial Worksites?
As technology continues to advance at an unprecedented pace, digital twin software has emerged as a revolutionary approach to optimizing and streamlining various aspects of an industrial worksite.
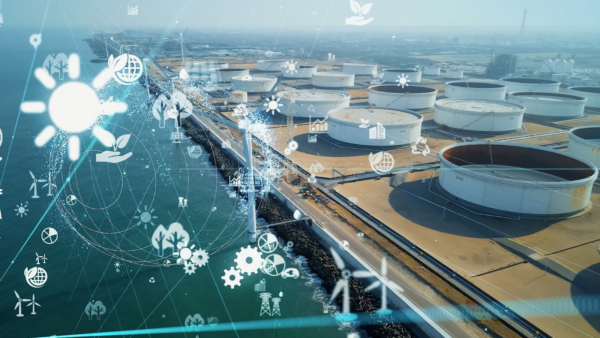
The Relationship Between Digital Twins, IIoT, and Worksite Optimization
The Internet of Things refers to an ever-growing network of internet-capable devices that can communicate with each other. Smartwatches, fitness trackers, smart speakers, smart doorbells, thermostats, and pacemakers are all examples of commonly-used IoT devices.
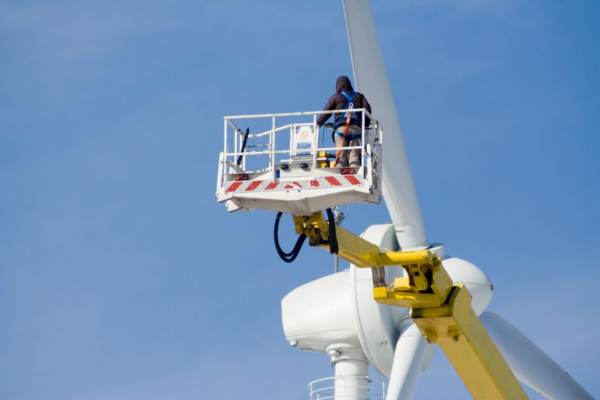
10 Ways to Improve Your OEE
Understanding the components of OEE (Overall Equipment Effectiveness) can help you drive continuous improvement initiatives to boost equipment effectiveness and efficiency, resulting in increased profitability.
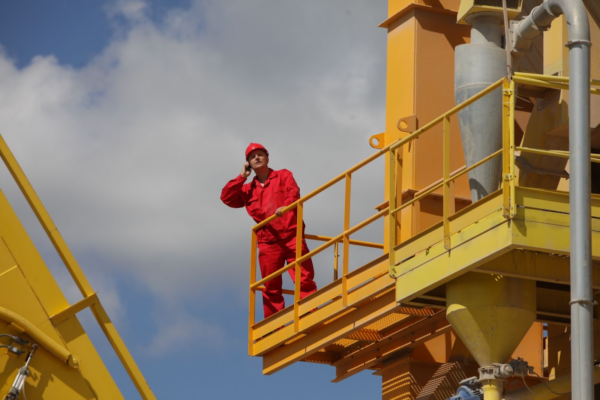
OEE Meaning: What is Overall Equipment Effectiveness?
Overall Equipment Effectiveness (OEE) is a crucial metric for evaluating the efficiency and productivity of your manufacturing processes.
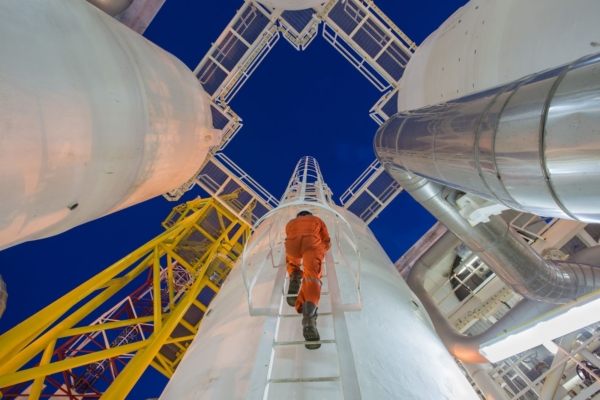
5 Ways Digital Innovation is Creating Safer Worksites for the in the Chemical, Oil & Gas and Refinery Industries
One thing is clear: the impact and importance of digitization in the chemical, oil, and gas industries cannot be overstated.